The company’s investment consists of two Kalmar ECG 150-12 electric forklifts and a charging station with extra battery packs. Each truck uses one battery at a time. The other
forklift remains available as a reserve to efficiently recharge the battery pack and enable continuous driving around the clock.
“We have installed an automatic charging system that shows which battery should be used when it is time to change. Choosing the right battery is extremely important for a battery’s lifespan, as the batteries must be rested before use. Thanks to the new system our drivers don’t need to calculate or keep track of the battery charge. Our automated process is controlled via lights and indicators that show which battery should be used next”, says Joakim Jonasson.
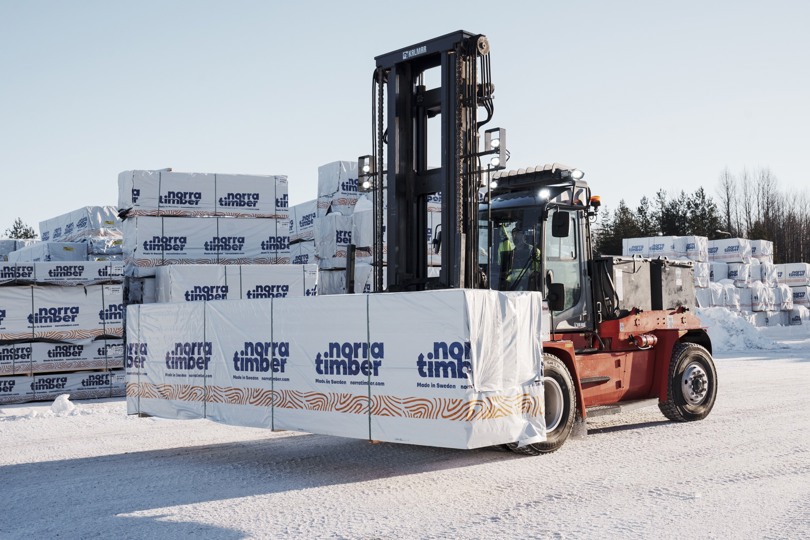
He believes one of the major advantages of the transition to electric forklifts is the positive impact it has on the environment. By reducing the use of diesel and using electric vehicles instead, Sävar Sawmill has decreased its carbon dioxide emissions by 144 tons per year - saving 60,000 liters of diesel that would have been used in two comparable diesel forklifts. As a result, diesel consumption has been reduced by 11 percent, making the sawmill a more sustainable business.
“An electric forklift consumes significantly less electricity than a diesel one consumes diesel, which means the investment in electric vehicles is more sustainable in the long term. We
benefit financially and the investment helps us achieve our sustainability goals. It’s a win-win”, says Joakim Jonasson.
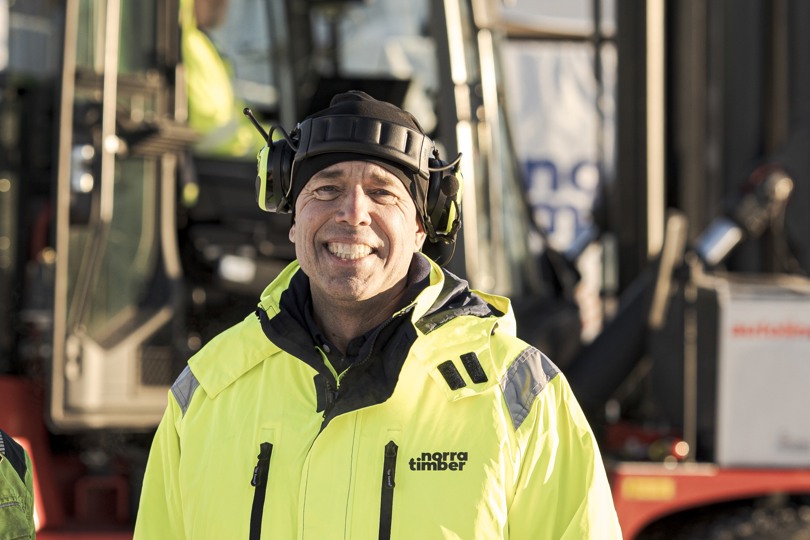
Reduced oil consumption
Oil consumption has also been significantly reduced, as the electric forklifts need neither engine oil nor gearbox oil and require fewer filters. They also need less maintenance compared to internal combustion engine trucks.
“Around 70 liters of oil are used for every 1,000 operating hours for a motorized forklift. For our electric forklifts oil consumption is zero. Operating them is significantly more environmentally friendly”, says Joakim Jonasson.
The new forklifts also offer advantages in terms of the company’s working environment. They are quieter and easier to drive and control compared to traditional forklifts. They also withstand the cold well – even in extreme conditions when temperatures drop down to minus 30 degrees. The new electric forklifts even offer better thermal comfort control than conventional vehicles, thanks to a special heating system.
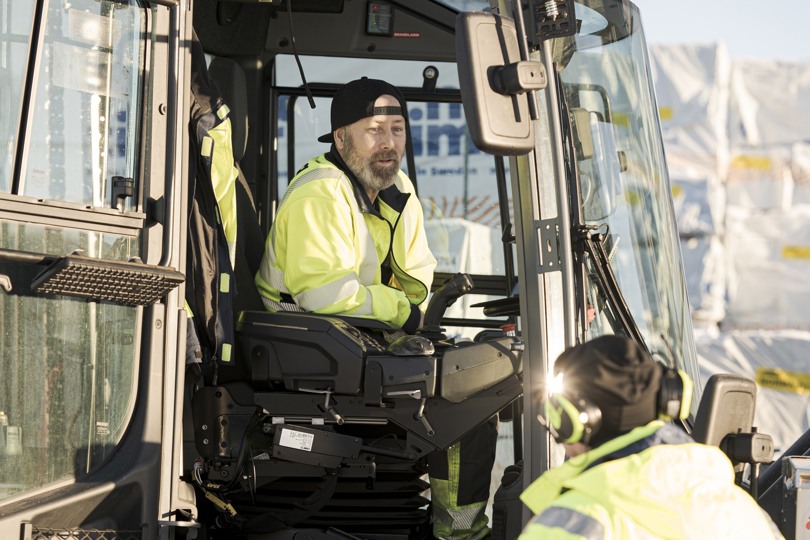
The use of electric forklifts is still relatively new within the sawmill industry, and to date only a few companies have incorporated them into their fleets.
“We will continue heading in this direction as part of our ambition to remain innovative and shape the future of our industry”, says Joakim Jonasson.